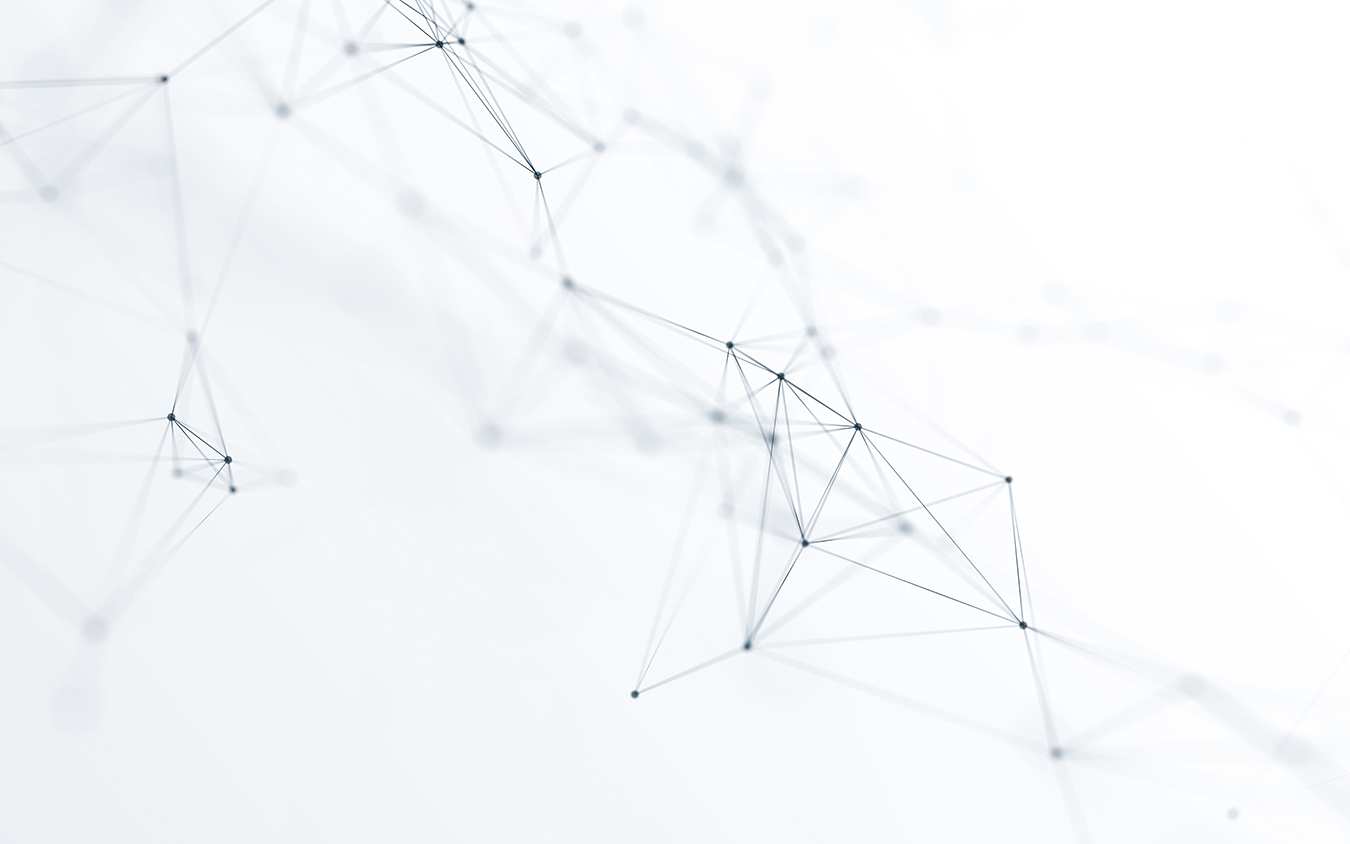
protec carrier systems
machinery
High Temperature Ceramic Chuck
ProTec®'s high temperature electrostatic chucking solutions are used in vacuum and atmospheric processes for the fixation of wafers, glasses or foils. The design is customized to your specific needs. Thereby, it is e.g. possible to achieve high cooling efficiencies in rather hot coating or etching applications even under vacuum atmosphere. Furthermore, in applications where the temperature needs to stay hot to achieve the desired coating functions the HT electrostatic chuck is the solution of choice. Depending on the application the high temperature electrostatic chuck can be used in an Inline or Cluster system.
Typical Applications
-
High temperature suited up to 300 °C, special version > 300 °C
-
100% customized in size, shape, functionality to best customer benefit
-
Size starting from very small 10x10mm² to large formats like Gen 10.5
Recommended Processes
-
Handling
-
PVD / Sputter
-
Plasma Cleaning
-
Ion Beam Etching/Trimming
-
Ion Implantation
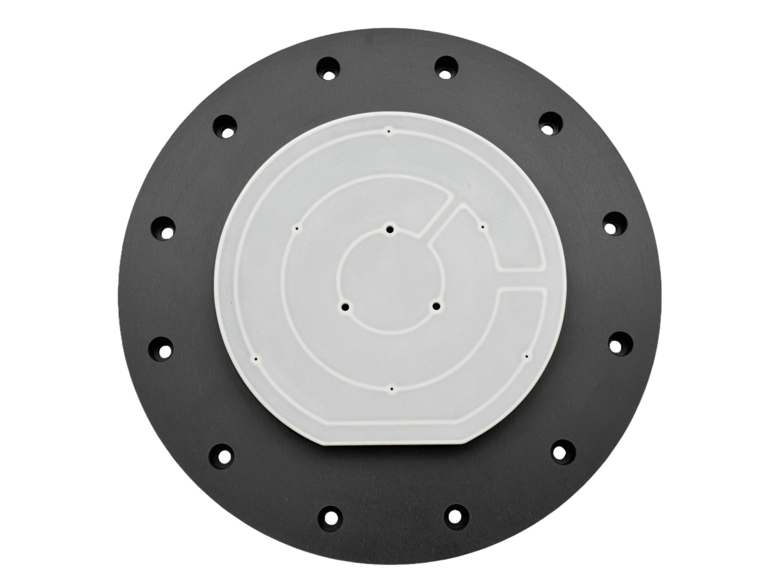
During the wafer processing the wafer needs to be transferred back and forth from the cassettes to the tools and also inside the tools from one station to the other. For fragile substrates this is already challenging, because they tend to break or get cracks, which can lead to future breakage. Also bowing of thinned substrates brings a lot of trouble for all tooling because they are usually not designed for this very special operation. Temporary bonding with our T-ESC® is a great help here as the processing tools only recognize a standard wafer and trouble with handling. Therefore, wafer breakage is eliminated.
Basically processes starting with a solid or liquid phase forced into the gas phase and building a solid again are called Physical Vapor Deposition. Sputtering is the most famous among them. Ions are accelerated and hit a target material. The ion bombardment results in free particles from the target material. These particles form a conformal layer on the substrate. There are different methods for the sputtering process depending on the target material and the desired layer properties, e.g. by adding reactive gases into the chamber, a combination of target material and gases build the layer on the substrate.
Another option is to heat a material until it gets into the gas phase and then guide it to the target substrate. This is called evaporation.
Plasma Enhanced Chemical Vapor Deposition usually uses temperatures which are lower than in a pure CVD step. A plasma leads to a split of the reactive gases, which are then deposited on the substrate.
During the Organic Vapor Phase Deposition (OVPD) organic material is heated up and evaporated. Then, the molecules are mixed with a gas which is blown on the substrate's surface. The substrate is actively cooled and the organic molecules build a thin film by condensing on the substrate's surface. The active cooling inside the vacuum atmosphere is greatly improved by using ProTec®'s electrostatic chucks.
Chemical Vapor Deposition uses gases to deposit layers on the substrate. Depending on the specific type of CVD, different temperatures and materials are used, leading to layers which vary in density and stability according to CVD type. The higher the temperature, the better the layer properties and usually the longer the processing time. However, not all substrate materials or already built structures can withstand the high temperatures. Therefore, either cooling is needed for the substrate or a low temperature CVD process type has to be chosen.
Plasma cleaning or ashing is usually used to clean the substrate's surface from residues of resist or other contamination. The gas is ionized and reacts with the resist forming ash which is pumped out of the chamber by vacuum pumps.
Reactive Ion Etching is a process where ions are accelerated onto the substrate hitting the surface and creating free particles. Depending on the chosen gases the ions are more reactive to different materials generating a selective process. However, the bombardment is creating damages, which can lead to a healing process afterwards.
The Deep Reactive Ion Etching is usually a mixture of etching and passivation layers to generate deep and sharp holes or pillars. The etching and passivation are done in a sequence.
The substrate is bombarded with an Ion Beam which removes the surface material. The removal is extremely precise.
The substrate is bombarded with ions which will stop inside the crystal structure and form doped regions. Usually, this is only wanted in specific parts of the wafer, so that the rest is covered by a mask and the depth of the ions can be controlled, as well.