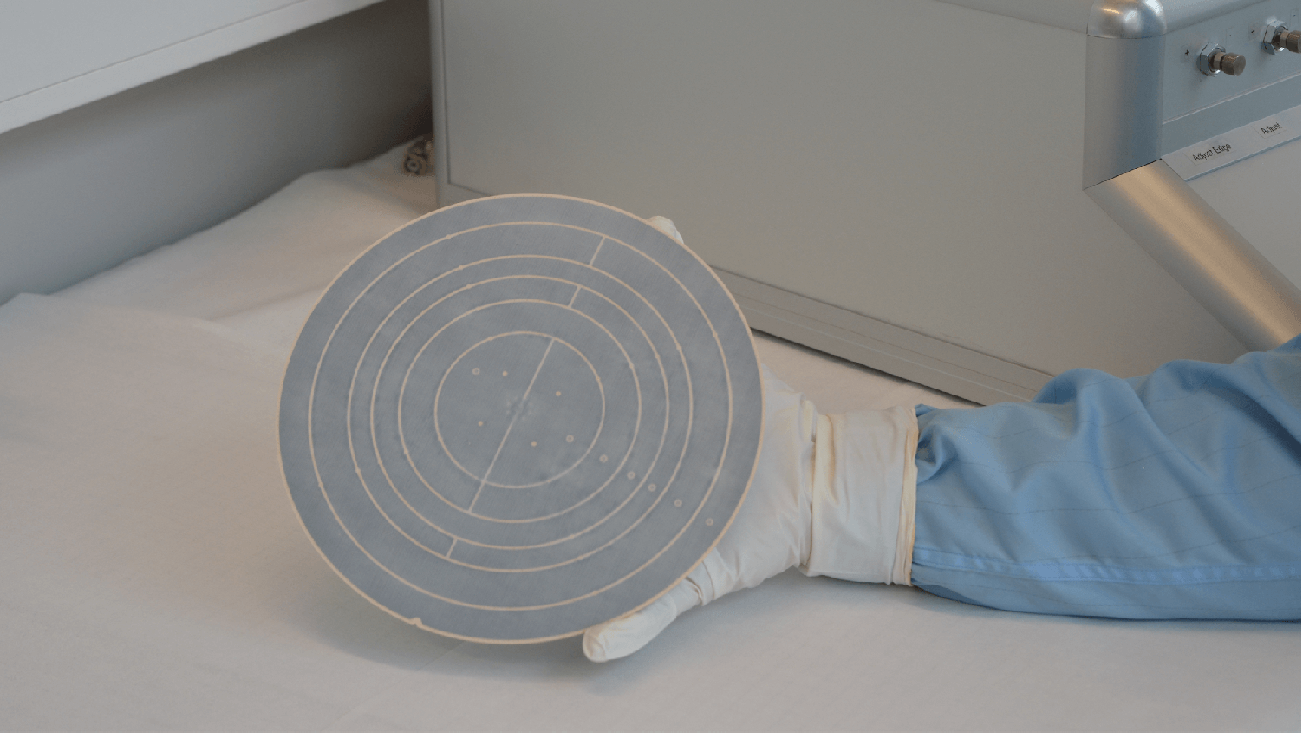
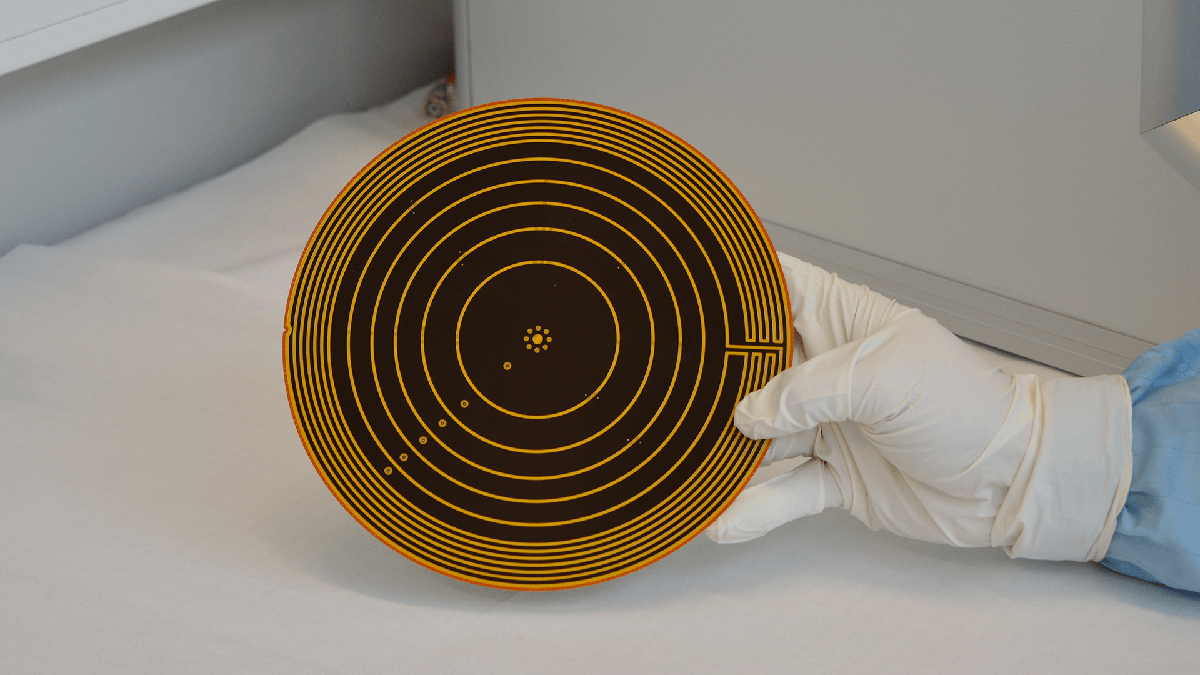
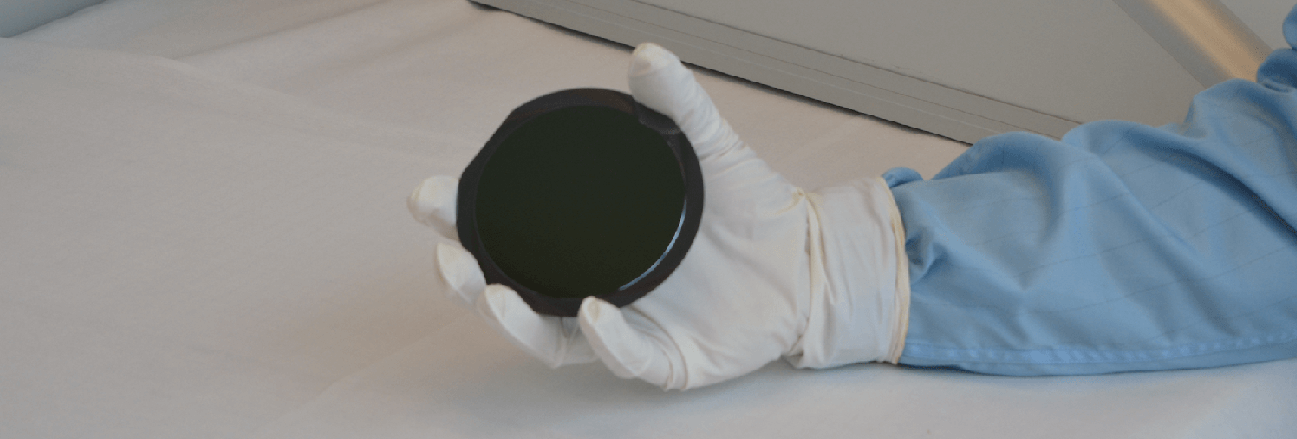
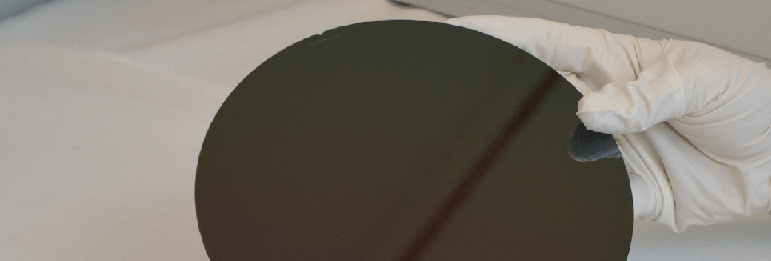
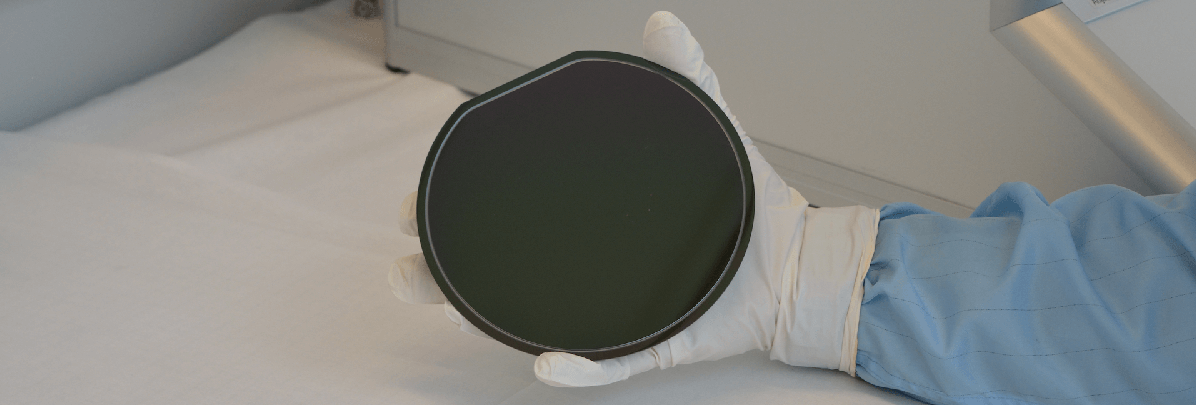
Transferable Electrostatic Carriers
The Transferable Electrostatic Carrier (T-ESC®) is an adhesive-free temporary bonding method that enables the safe and reliable processing of fragile substrates and various materials such as ultra-thin substrates, GaAs, InP, LN, LT, thin silicon, thin MEMS wafers and many more. The basic concept behind this sustainable temporary bonding technology involves the use of electrostatic forces to chuck device wafers onto mobile rigid Carriers (T-ESC®).
These wafer-carrier packages can then be handled and securely processed like wafers of standard thickness through existing machines within the customer facility. Therefore, existing cassettes, handling tools and fabrication equipment can be used without modifications. Additionally, the warping and bowing of thin and ultra-thin substrates are eliminated. The Transferable Electrostatic Carriers are available in the standard sizes from 2" to 12" and in customized shapes adapted to the intended application.
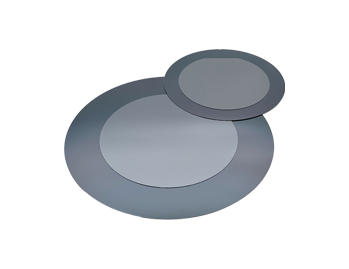
The Adapter Carrier
Each T-ESC® type is offered as an adapter version that allow machines to process device wafers of different diameters and forms. The smaller device wafer can be temporarily bonded to an Adapter Carrier and is held in position by electrostatic forces. For example, a 4”/8” Adapter T-ESC is suited to fixate a 4” wafer on an 8” Adapter T-ESC.
The package of a 4” wafer and an 8” Adapter Carrier can now be used in the intended equipment, e.g. an 8” Stepper. The Stepper tool recognizes a standard 8” substrate and can now process the smaller 4” wafer sizes.
(MEMBER OF THE T-ESC® FAMILY)
Polymer T-ESC®
The Polymer Transfer ElectroStatic Carrier (Polymer T-ESC®) is a low cost carrier solution for processes without high heat impact where only handling is in focus. Additionally, it can be used for wafer flipping applications.
As an option there is a modified version of this mobile electrostatic carrier which is suited for spin etching in SEZ-Tools with Bernoulli Chucks. The special shape of the Polymer T-ESC® enables carrying a thin substrate through the process without creating residuals between the carrier and the thin wafer during the etching process.
Polymer T-ESC®
Typical Applications
- Compatibility with existing handling systems (transport cassettes, vacuum, Bernoulli or mechanical end effectors etc.)
- High flatness
- Re-usable
- Sizes from 2" to 12", customized shapes and features possible
Recommended Processes
- Handling
- Probing
- Spin Etching
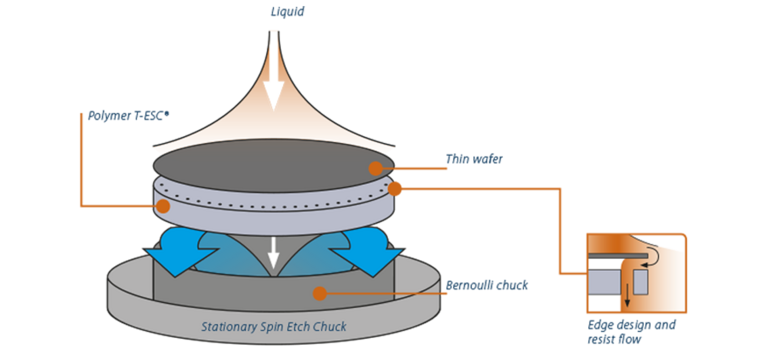
Handling
During the wafer processing the wafer needs to be transferred back and forth from the cassettes to the tools and also inside the tools from one station to the other. For fragile substrates this is already challenging, because they tend to break or get cracks, which can lead to future breakage. Also the bowing of thinned substrates brings a lot of trouble for all tooling because they are usually not designed for this very special operation. Temporary bonding with our T-ESC® is a great help here as the processing tools only see a standard wafer and trouble with handling. Therefore, the wafer breakage is eliminated.
Spin Etching
Spin etching is following the same principle as spin coating. The substrate is clamped to a chuck and during the spinning, etching chemicals are jetted to the surface.
Probing
Various probing methods exist. They are used to check the substrate´s or device´s functionality, e.g. there are optical inspection or electrical probing.
Our Machines
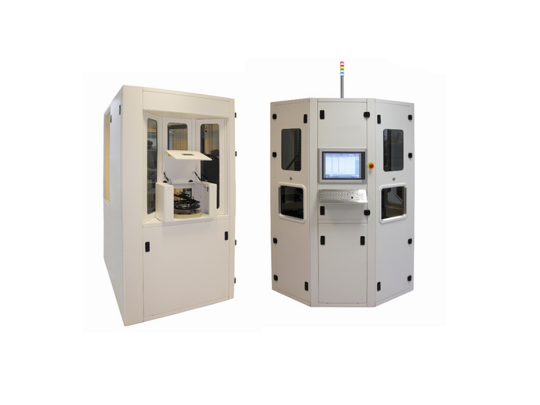
ACU 3000
A fully automated electrostatic chucking/ dechucking unit with up to 120 wafers and/or T-ESC® packages per hour, guaranteeing the highest yield during handling and many diagnostics features.
Learn More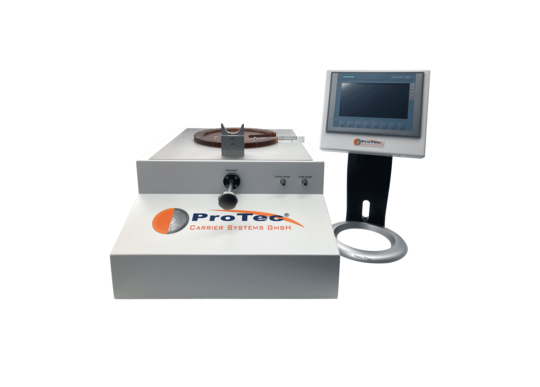
MCU 3000
A manual chucking/ dechucking unit of thin and ultra-thin substrates on carriers (T-ESC®s) for flexible sizes from 4”/6” to 8”/12” with a high flexible mobile handling tool and diagnostics features.
Learn More